Guía completa para la instalación de equipos logísticos
Make Your Warehouse Faster, Más inteligente, and Safer
Logistics Equipment Installation is key as customers expect fast and accurate delivery in today’s fast-moving world.
La instalación del equipo logístico requiere más que colocar máquinas: necesita un plan, las herramientas correctas, y expertos capacitados. Esta guía explica cada paso claramente.
Logistics Equipment Installation applies whether you’re upgrading a small warehouse or building a large fulfillment center — this guide will help.
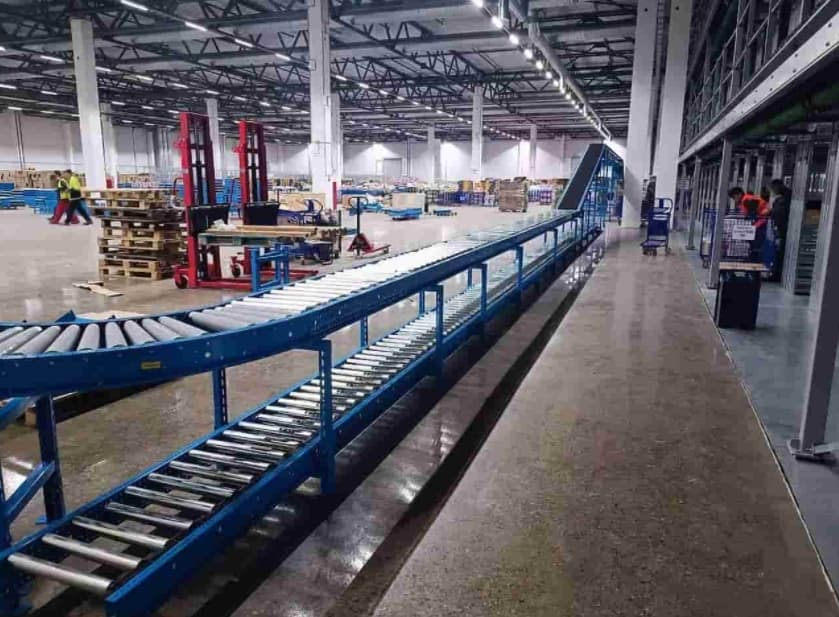
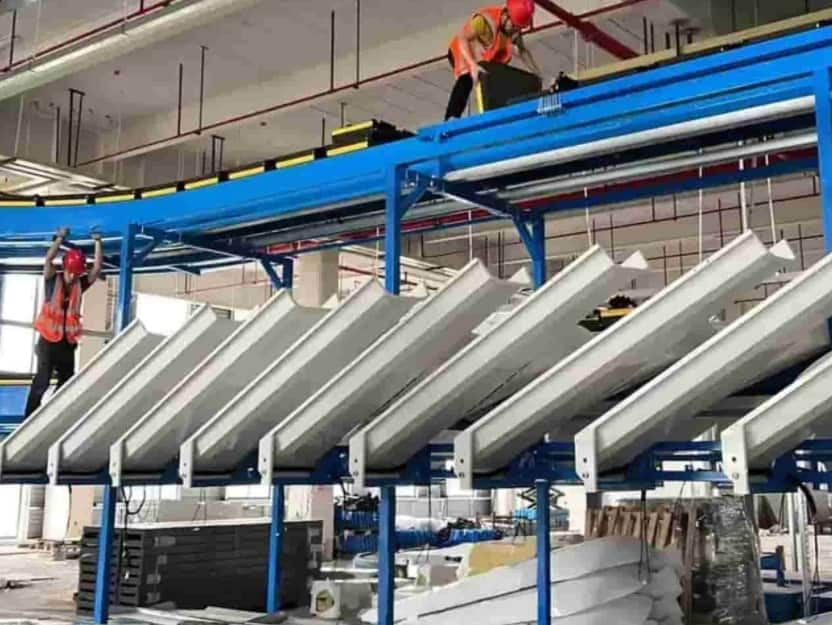
What Does “Logistics Equipment Installation” Mean?
Let’s keep it simple. Logistics equipment is anything that helps you move, sort, or store items in your warehouse. This includes:
Conveyor belts
Sorters
Lifting machines
Racks and shelves
Automated storage systems
Installation means setting up this equipment in your space. It includes planning, building, wiring, pruebas, y entrenamiento.
Done well, it can speed up your work, make your team safer, and help you serve customers better.
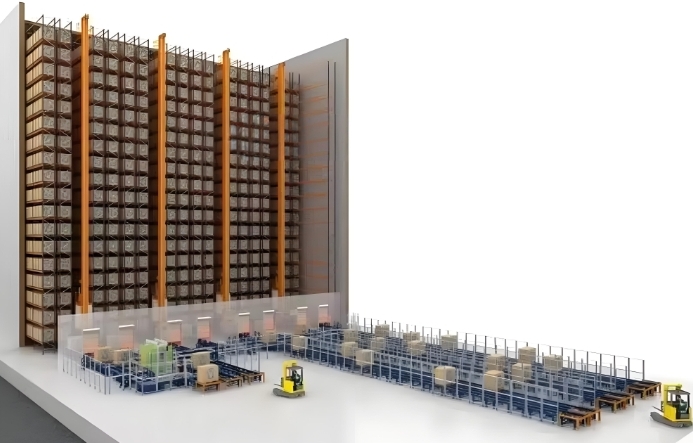
Step 1: Planning — The Most Important Step
Planning is the first and most important part of the installation process. Without a good plan, you could waste time and money. Here’s what to think about:
Measure Your Space
Before you install anything, you need to know your space. Measure your warehouse. Think about where items come in, where they’re stored, and where they go out.
Map the Flow
Plan how goods will move from one area to another. A smooth flow reduces delays and keeps workers safe.
Choose the Right Equipment
Not every warehouse needs the same tools. Por ejemplo:
A conveyor belt helps if you move a lot of small boxes.
A pallet shuttle system is great for large, heavy items.
Sortation machines help you handle high order volume.
Plan Your Budget and Timeline
Write down how much you want to spend and how long it should take. Add extra time in case something takes longer than planned.
Follow Safety Rules
Check building codes, fire safety rules, and equipment standards. Talk to local safety inspectors if needed.
Planning well now means fewer problems later.
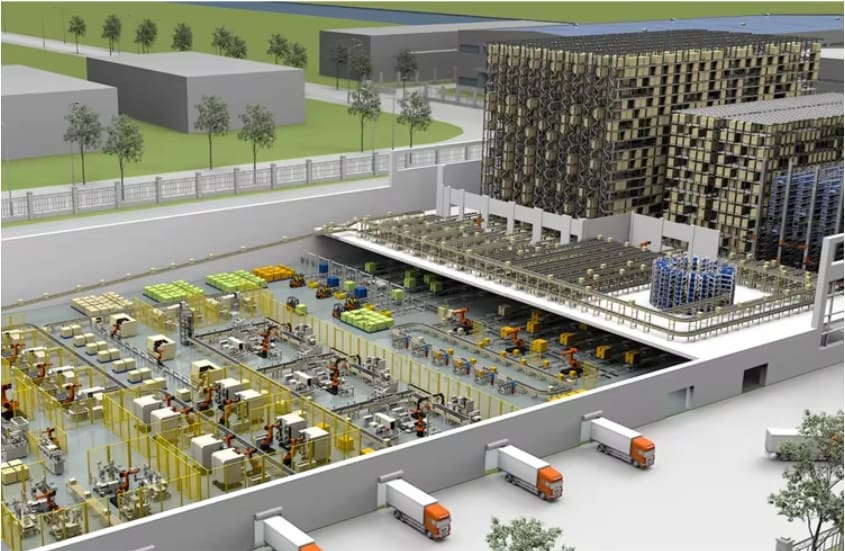
Step 2: Types of Logistics Equipment
Different warehouses need different tools. Below are the most common types of logistics equipment:
Equipment Type | What It Does | Best For |
---|---|---|
Conveyor Systems | Moves items across the warehouse | Order packing, sortation hubs |
Stacker Cranes | Stores items high up in racks | High-bay or cold storage |
Picking Systems | Helps staff find and grab items faster | eCommerce, retail fulfillment |
Sorters | Directs items to the right place | High-volume delivery centers |
Smart Shelving Units | Stores and finds items automatically | Smart or robotic warehouses |
This equipment can cut errors, boost speed, and reduce labor costs.
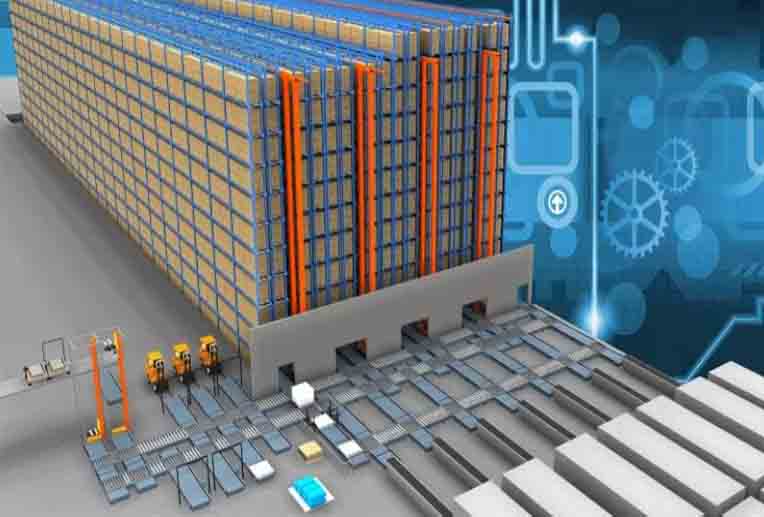
Step 3: The Installation Process
Once you have a plan and the right equipment, it’s time to install. This usually happens in a few stages:
1. Site Prep
Clean the space
Level the floor
Mark where equipment will go
Make sure power, internet, and safety systems are ready
2. Install and Assemble
Unpack equipment
Set up racks, shelves, or machines
Bolt or anchor them into the floor
3.Connect Power and Controls
Wire machines to electricity
Install software or control panels
Connect to your warehouse management system (WMS)
4. Test Everything
Run a test with real items
Check for smooth movement, speed, and accuracy
Fix any errors or issues
5.Train Your Team
Teach workers how to use the new systems
Review safety steps and emergency stops
Give simple, clear instructions
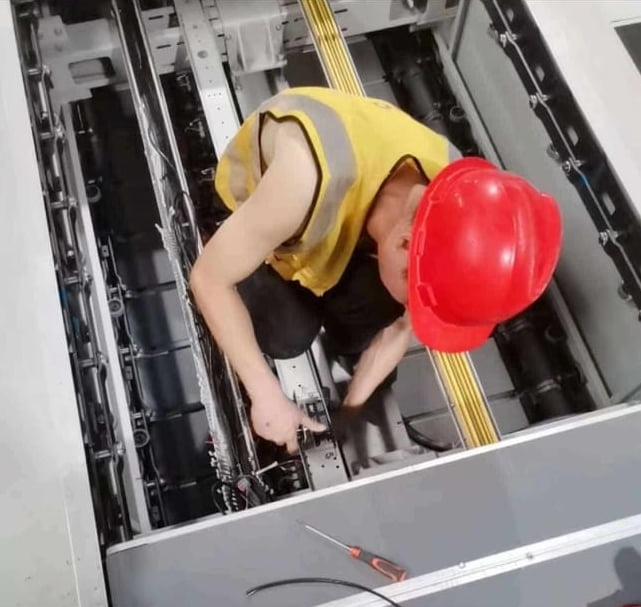
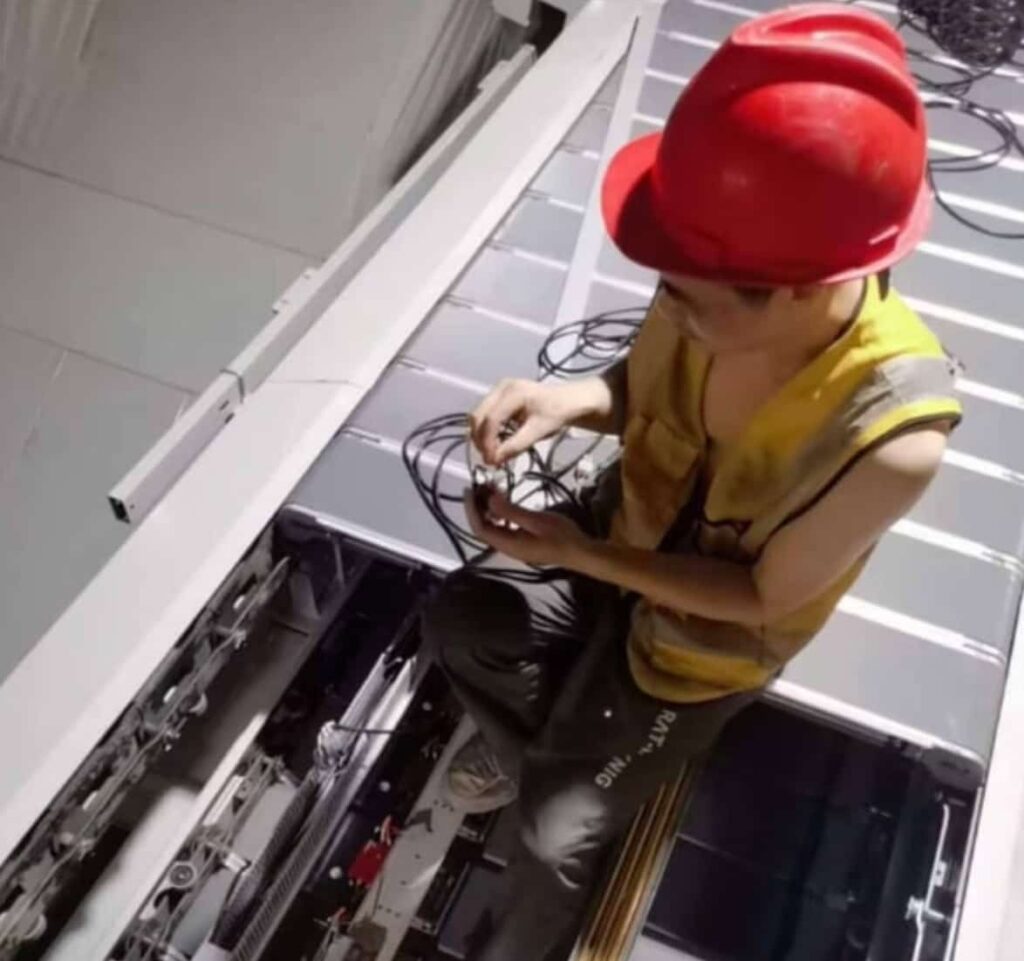
Step 4: Check, Maintain, and Improve
Your equipment is running — great! Now keep it that way.
Regular Maintenance
Check your machines often. Tighten bolts, clean belts, and inspect wiring.
Make a checklist and stick to it. It’s cheaper to fix small issues than to wait for a big failure.
Staff Training
Keep training your team. New workers need to learn the systems. Older workers may need updates.
System Updates
As your business grows, you may need to change the setup. Plan for upgrades in advance.
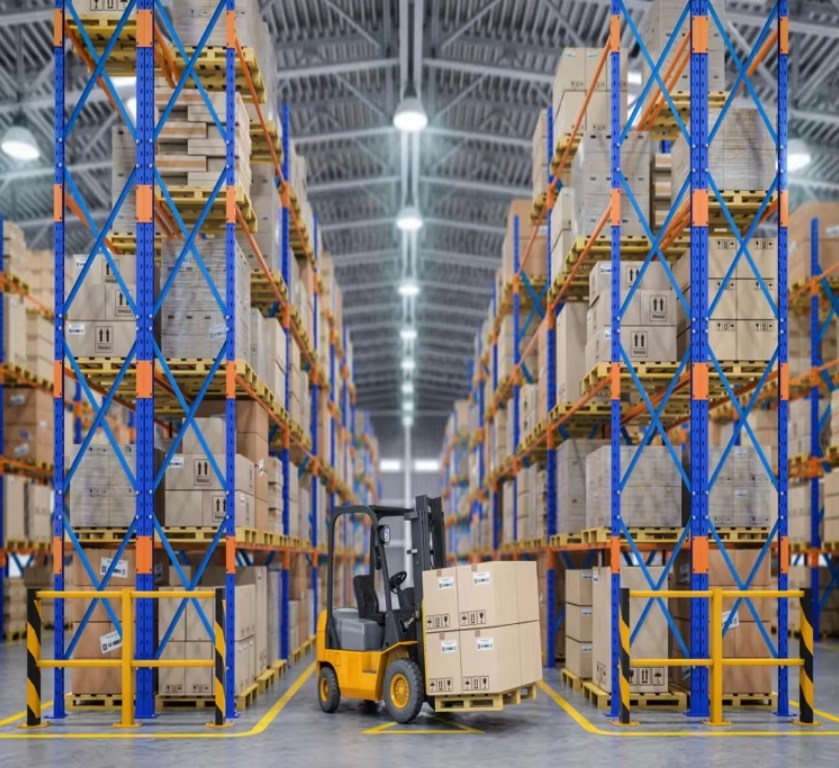
❓ Common Questions (FAQs)
Can I install logistics equipment while my warehouse is running?
Yes. You can do it in steps or work during nights or weekends to avoid downtime.
Is it safe to install the equipment myself?
For small tools, maybe. For large machines or automation, always use trained professionals.
What happens during professional installation?
They’ll deliver, install, test, and train your team. Some also offer post-install support.
What if something breaks later?
Ask if your provider includes warranty and support. Maintenance contracts can also help.
Why You Should Work With Pros
Installing logistics equipment isn’t like building furniture. It requires skill and safety knowledge.
A professional team can:
Finish the job faster
Avoid damage to equipment
Help you stay compliant with laws
Train your team the right way
Provide long-term support
It’s worth the investment.
📣 Final Thoughts: Get Ready for a Smarter Warehouse
Installing logistics equipment is one of the best things you can do to grow your business.
It helps you:
Move goods faster
Handle more orders
Keep your team safe
Lower your costs over time
But it only works when the setup is done right. Plan well, install smart, and maintain it over time. Want help? Talk to our experts and schedule a free warehouse assessment today.